

|
|
Big Trains
Large, Large Scale Track - Part I
Aug 13, 2002
By Rick Henderson LSOL.com Associate Editor |
Author
Bio
Track laying in any scale of railroading is one of the more important aspects of the hobby.
|
Track laying in any scale of railroading is one of the more important aspects of the hobby. However, too often people take short cuts here and wonder later why their trains don't run well. Take time to plan out your route, radius, grades and then lay track correctly the first time. This will save a lot of aggravation later on. In 7 1/2" gauge, you and visitors will be riding on the track so you want it done correctly.
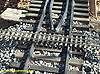 Click for larger picture | Most of the track used in the "G" scales comes sectional and pretty much ready to install. The sections that are flexible most often use tie strips that you slide the rails onto and the track is held in gauge. Track laying in 7 1/2" scale is a little more labor intensive. While it is true that you can actually buy ready-made track sections, they are rarely used due to costs. Rail is normally purchased in 10' or 20' lengths, then you buy pressure treated wood in 2x4-10' lengths and cut this into 8 sections, 15" long each for the ties. You also need 124 screws and washers for each 10' track panel built. |
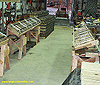 Click for larger picture | After the ties are cut and stained, you place them into a 10' track-making jig, which holds 31 ties correctly spaced apart. The two rails are placed on top of the ties and are held in place with rail gauges mounted on blocks between the ties in several locations. The rail is held down tight against the ties with temporary cross clamps over the top of the rail. |
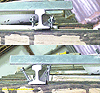 Click for larger picture | When screwing down the rail to the ties, two things are important. Make sure the screws go straight down into the tie and not at an angle, the same as when driving a spike on the prototype railroads. When being installed, one of the rails will have to be slid to match the end of the previous section. Screws that are installed at an angle can allow the tie to fall off the rail when loosened to slide and they do not hold gauge properly. |
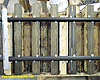 Click for larger picture | Also make sure the pattern used on one tie is followed for every tie in that panel. The screws are the opposite pattern on each rail. This is to ensure that the proper gauge is kept should the ties move. Notice the consistent pattern on every tie. In this sample, the outside screws are towards the left side of the tie while the inner [gauge side] screws are towards the right side of the tie. When it is time to slide the rail, it will slide very easily towards the side the inner screws face but will pinch if you try sliding the opposite direction. |
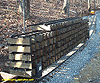 Click for larger picture | After track panels are built and removed from the jig, they need to be transported to the end of the line where you are laying track. If you have 10' long flat cars you are in luck. Our club has no 10' cars but there is a set of logging type disconnects. These work very well for transporting the panels and other long material to their destination that can be a few thousand feet away from where they were built. |
Laying the Track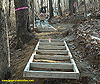 Click for larger picture | Having a solid roadbed is extremely important in 7 1/2" scale, or any scale where you actually will ride your train. If it is not level across the rails, then your passengers on your cars will feel the tipping to one side and become nervous. Getting the rails level starts in the ground preparation work. The ground must be level with drainage provided along the sides where needed. It also needs to be tamped firm so it will not erode away, undermining the ballast and track. Next a roadbed form is placed and leveled side to side and set to the correct grade end to end. We use a special construction section of track across the frame attached to the end of the last installed track section. This allows the ballast cars to come over top of the frame and drop ballast. |
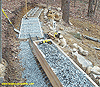 Click for larger picture | The ballast used is 1" to 1 1/4" rough edged rock. The ballast in the frame is tamped tight and level before the frame is removed. Once removed, we now have a 3 1/2" bed of ballast, which is important so that water drains quickly away from around the ties. Ties that have standing water around them will not last. The track will be laid directly on this sub-roadbed. |
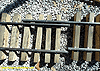 Click for larger picture | The new track panel is positioned by lining up the panel with the short rail from the previous panel. Even if it will be a curved section, we keep the new panel straight until the one rail has been slid in place. All of the screws are removed from the ties that will hold the end of the previous section. The rest of the screws along that entire rail are loosened just enough to allow the rail to be slid easily away from the previous section. When joining sections, you want the joints to be offset from each other on the opposite rails, especially on curves. This helps keep the sections from trying to separate and keeps the joints better aligned along the rails. |
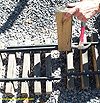 Click for larger picture | The rail is tapped if it cannot be moved by hand. It is important that the rail that is not being moved is screwed down tight to the ties. You want to move it far enough to mate up with the end of the long rail from the previous track section. If the panel you are working with will curve, you have to consider that curving will shorten or lengthen the rail position after it's curved. Once panels are curved, the rails are hard to slide. |
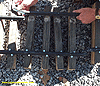 Click for larger picture | The rail joiner is added by sliding it completely onto one rail and then after the rails are aligned, sliding 1/2 of the joiner back onto the adjoining rail. Slip joiners are the most common and have an advantage of allowing the track some room for expansion and contraction during the seasons. |
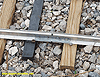 Click for larger picture | Joint bars, a more expensive option, are fundamentally better at keeping the ends of the rails aligned, especially on curves but they do not normally allow much for expansion. The joint bars pictured here actually have oval shaped holes milled in them, which will allow for some movement. Also note in the picture they are experimenting with a new plastic composite tie. |
Once the track is connected and aligned properly then the screws on the loose rail are tightened down. This will actually hold the section in place some, even if curved. Ballast is then added between and on the outside of the ties. This helps hold the track in place once it is tamped down between the ties. An average of 4 loaded ballast carloads is used in every 10 feet of track.
The natural tendency of the rail is to always go back to its straight alignment. The only way to overcome this is to use a rail bender, a device usually made of three rollers that you run your rail through several times, increasing the radius slightly on each pass, until you have it curved to the radius you are laying. The drawback to using a rail bender is that you either have to make a curved track jig for every radius of track you will be laying, or you lay the ties on the sub roadbed of ballast and then lay one of the curved rails, screw it down and then lay the other rail, gauging off the first rail. This is slower and harder since you have to be on the ground instead of standing at a waist high jig back in the shop.
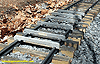 Click for larger picture | Once you have laid, aligned and ballasted the track you are not done. In fact, track work is never completely done. You have to maintain it on a regular basis. Track can become out of gauge, especially on curves. With the weight of the trains always pushing out on the outside rail of a curve, it is possible that the screws will be pushed out. If they were put in at an angle, they will move out easily, widening the track, putting it out of gauge. Notice that track can go out of gauge in a very short distance. Sometimes the gauge can actually be affected if the radius of the track changes by moving around in a loose ballast roadbed. |
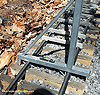 Click for larger picture | The level of the track can change as ballast and the ground settle. This is very common in the first year or two after initial construction. A track-leveling tool is used to level the rails, and then the ballast must be re-tamped between the ties so track does not slip down again. |
In Part 2 we will cover Crossing Bridges, Special Needs of Large Scale Track and more!
Top of Page
|
|
|
IMPORTANT LINKS
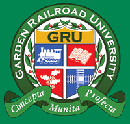
Get Your Official Diploma
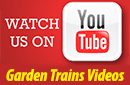
Watch New Videos
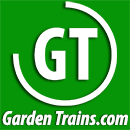
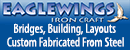
New Products Online
|
|