Track & Bridges
"Big Guys" Roadbed
Apr 23, 2003
By Dwight Morgan |
Author
Bio
I wanted to go with something of a prototypical ballasted roadbed so the rails would be allowed to expand and contract with out tearing out anchoring devices. My reasoning was, "The big guys do it this way because it works."
|
When I decided to start a Garden Railroad, I had no idea what I was up to. I felt that I wanted to go with something of a prototypical ballasted roadbed so the rails would be allowed to expand and contract with out tearing out anchoring devices. My reasoning was, "The big guys do it this way because it works." I figured that indoors on small scale railroads there was not a big temperature fluctuation so they would not have a problem, but outdoors was an entirely different story. I read what I could find regarding grades and methods of leveling. I decided that the best thing I could do was use a water level and some surveyor's stakes to find out what the land had in store for me and then see what I could do with it. My wife, who was the experienced modeler, said to use curves to add interest when laying out the track plan. I figured this meant I could put in lots of curves to make the grades less. I found out that too many curves causes derails more often than not. It was now time to figure out what to use for ballast and how to contain it so it would support the rails and not be washed out by 1:1 scale water when it rained. I had heard that you could dig a ditch and fill it with gravel and lay the track on that. The problem was that some places I would have to fill in a low spot by just about as much depth as the ditch would require me to dig out. If the ditch were to hold the gravel I would have to place the fill and pack it down, let it weather a season or more, then dig the ditch. Otherwise, the sides of the ditch would not hold.
I decided to use 4" plastic 'bender board' edging for the sides of my ditch. This would keep the sides from collapsing when the ground was not packed as solidly as desired. It would also serve to hold the ballast in when the ground was a little lower than the top of the ballast desired. I could then add dirt on the outside of the "ditch" later to make it right. During installation I learned that it pays to use lots of plastic pegs, both on the inside and outside of the edging to keep the distortion of the edge down and the sides vertical. The plastic gets very pliable in the heat of a sunny day and will not stand up against the pressure of the dirt outside the ditch before it is filled with ballast or the pressure of the ballast if there is no dirt outside the ditch. Once a section of roadbed is complete a lot of the pegs can be removed for use on another section of construction.
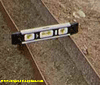
I used a level to keep the top edges aligned as I went. Click for larger picture I was also concerned with the possibility of weeds growing up through my tracks. I did not want to be pulling weeds out of the track all the time, with the possibility of removing ballast at the same time, instead of running trains. I thought of sterilizing the soil under the track, but all the chemicals indicated that they might be detrimental to plants I wanted in the vicinity of the track, so that was out of the question. I then "discovered" a fabric that is intended to keep weeds from growing through it while letting water trough in the other direction. What a great idea!My ballast would be crushed granite (#5 roofing gravel) from a local decorative stone supplier. It comes in 80 pound bags, much like cement products. When I started thinking of how many bags I was going to have to haul to build my railroad, I got tired. I thought I could cut down the number by making the ditch shallower. However, since the edging comes 4" wide I would have to cut it and that would not be an easy chore either since the stuff is made to be indestructible. I also found that when I started digging my ditch I had a lot of rocks which caused the bottom to be uneven and not so firm by the time I got finished dealing with them.
I made a sieve out of 2 x 4s and 1/4" hardware cloth ( the stuff that goes on attic and crawl space vents) and sifted the dirt I dug out of the ditch. With this sifted dirt I filled in the bottom half of the ditch and packing it down nice and firm with a piece of 2x4. I also use a flooding method to level it out where there was no grade to worry about. This process gave me a 2" deep ditch with a very firm base.
I bought a 50 foot roll of weed barrier 3 feet wide and some 12 d galvanized nails to do my weed prevention. Since my ditch is about 5 or 6 inches wide (not a precision project) I cut strips of weed barrier 7 inches wide off the end as I rolled out the weed barrier. This allowed me to install 3 feet at a time with the edges rolling up the sides of the ditch. A single galvanized nail held the end in place and I would overlap about 4 inches and stick a nail through when I added the next piece. After I got a few sections of weed barrier down I would fill the remaining 2 inches of the ditch with ballast and tamp it down nice and firm. (On the curves, I would cut darts into the inside edge of the weed barrier allowing it to follow the curve without bunching up). 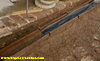 Sifted dirt and weed barrier installed in ditch. Click for larger picture
Once the ballast is in place and up to the top of the ditch the track is placed on the firm surface and more ballast poured on top and spread about so it packs in around the ties inside and outside the rails. The roofing gravel has sharp edges which grip the ties and cut the fingers of your hands so I suggest fairly good leather gloves for this. Cotton gardening gloves do not last. 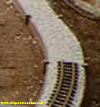 Ballast added above the weed barrier Click for larger picture
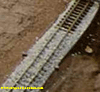 Track added , then more ballast to finish.. Click for larger picture
Since the track is laid at the top of the edging, switches can cross over it with no difficulty. The edging for the siding, spur or whatever is installed tight up against the existing edging and pegs installed to hold it together and in place while under construction. Once this is ballasted it to will take care of itself for the most part and the pegs can be removed so they do not interfere with the track. 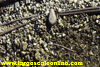 The lower piece of edging was added when the switch and track below were added. Click for larger picture
Over the years, when I have added parallel track I have often just added the new outside edging and left the old in the center of the resulting two rail roadbed.. This allows the ballast to be at slightly different levels.
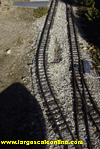 The left rail was added several years after the right was installed Click for larger picture
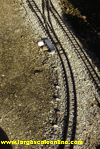 The lower switch is new. It was just a curve originally Click for larger picture
The pictures I have here were not taken with this article in mind, but rather as an aid to a conversational show and tell. I hope they are clear enough to show what I have described. When I have had to remove the ballast for any reason, the weed barrier provides an aid to getting the gravel without the dirt so it can be reused. I usually replace the weed barrier in such cases since it does deteriorate. However, over the nearly 8 years it has been in place, I have not had any weeds grow through it. I did have some aggressive bulbs come up and punch 1" to 2" holes in it and lift my track 4 to 5 inches off the roadbed though. That is a story for another time, like when you come to visit. I hope this is helpful to some of you. If you have questions, please feel free to e-mail me through the LSOL site or just place a question in the Track Workshop. Dwight Morgan
Top of Page
|