

|
|
Scratch & Bash
:
How-to's
More Stomper action on your railroad
Sep 17, 2002
By Mike Gray |
Author
Bio
Stompers are small, inexpensive, lighted, two speed AA battery powered 4-wheel drive toy cars that have a wheelbase perfect for 45 mm track.
|
 Click for larger picture
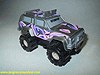 Click for larger picture
| Stompers are small, inexpensive, lighted, two speed AA battery powered 4-wheel drive toy cars that have a wheelbase perfect for 45 mm track. They have been around off & on for several years, marketed by several different distributors.
Latest reincarnation is by Tinco. This time they seem to be available everywhere for $4 - $5. For the money, they are surprisingly well engineered and operate trouble free. |
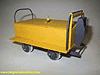 Click for larger picture
| Yes, there are similar vehicles out there but not so widely available or narrow enough to easily mount a RR type body on the motor block. So check out your local drugstore, discount toy store, Wal-Mart or K-Mart. Look for the bubble pack and purchase a few. Then, let's get started. |
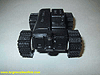 Click for larger picture
| Remove the toy body. What you have is a motor block with tires. Remove the tires by bending them until they pull off. Next, cut off the hubs. A Dremel tool with a cutting wheel works well. (Eye protection is a must with the cutting wheels as they easily fly apart). An alternate is a razor saw and manually cut off the hubs. Be careful not to damage the axle shafts. These shafts are needed to mount the speeder wheels. |
When stripped down, you will have a motor block with loose fitting square axles. Open the battery cover, then carefully unlatch and pry open the motor side cover. It will be a bit difficult the first time as the plastic cover is spot welded in a couple places. Be careful to keep the motor block upright during the cover removal. Inside is a double shaft motor and four worm gears.
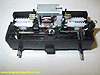 Click for larger picture
| Note how the worms are mounted in little pockets, in case they fall out. Place a bit of plastic-compatible grease on the worm gears and shaft ends and a drop of light oil where the motor shafts enter the motor. This lube will be sufficient for several hours running. If you do not intend to utilize the tiny light, snip off the wires while the motor block is open. This will extend run times a bit. |
Now that your motor block is stripped and lubed, you need to decide what will be mounted on it. This will determine the wheel size and mount arrangements. The Stompers were only meant to power themselves so rule out locomotives, critters and the like. However, what is left is a vast world of RR mow (maintenance of way) equipment from the early 1900's on. Within this group are speeders or motorcars. Until the 70's, railroads used them to transport track maintenance people and equipment. They are 4-wheel self propelled vehicles that run on rails and small enough so that one or more people can lift an end, to turn or remove them from the rails.
Today, most are gone from the railroads but they have reappeared as hobby vehicles. That is to our benefit as there are literally hundreds of pictures and information on the Internet at many web sites. Do a search on Google Images with speeder or motorcar. You will find plenty of images. Chase down the links with these images for even more images and information. Or do a search on NARCOA, the speeder hobby national organization. Hardest part will be to decide which body to put on that motor block.
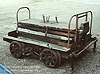 Click for larger picture
| You can go from a detailed scale body to a caricature. It is your RR. For our example model, the prototype is a vintage Fairmont S-2 once used by the former Copper Range RR in the U.P. of Michigan. The image is courtesy of Kevin Musser. With some liberties (the CRRR was standard gauge), this example is a 1:20.3 model that generally follows the S-2 lines. All speeders were relatively small, so scale is mostly set by the size of the speeder operator. However, for 1:29 to 1:32, the body overhang should be less as the prototypes were about the width of the track. Narrow gauge speeders (1:20.3) would overhang the wheels more. The operators need a place to sit! |
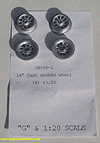 Click for larger picture
| Now that you picked a body type, a wheel decision is next. Speeder wheels are relatively small, 14" - 20" diameter. Ozark Miniatures makes some wheels in this range. The example uses OM-58-2 wheels. If you are building a caricature, even plastic RR car wheels will do. The Ozark wheels are metal and need to be insulated from the one piece motor block axles. Then, you can operate your creation on anyone's layout without fear of electrical short. |
For the Ozark wheels, obtain a length of 1/8" OD plastic tubing (Plastruct or similar). Drill out the wheel hubs with a 1/8" drill but leave about 1/32 " at the bottom. Easily done with a drill press but can be done manually with a pin vise. Be careful to drill straight in (Speeder will operate with a little wheel wobble but looks better without). Cut off 5/16" sections of the tubing and insert in the wheel hubs. Drill out the plastic tubing with a 3/32" drill.
Then, start the wheel / tubing onto the motor block axles. Fit will be tight. Continue pressing on the wheels with a vise. Go slowly and check the gauge either with calipers or against a good running large scale wheel set. Snug up to about 1.59" back to back or a little wider than the wheel set back to back. Put a battery in the beast and do a test run. If it derails, observe if it fell between the rail or climbed over. Adjust wheels in or out if necessary. When it runs well, a drop of ACC will lock the gauge in place.
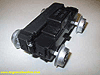 Click for larger picture
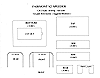 Click for larger picture
| That completes the basic motor block. Now on to the body. The bottom plate and other parts can be cut from styrene sheet. The enclosed drawing features full scale parts and suggested sheet thickness. One way to transfer the patterns is to print a copy of the drawing, cut the paper parts oversize and cement to styrene sheet with rubber cement. Use the score and snap method to cut the parts out. |
Score along the pattern lines with a single-edge razor blade or Xacto knife and straight edge. Position the scored sheet over a workbench or table edge and bend. Sheet will snap along the score line. Continue scoring and snapping until all parts are cut out. To remove the bottom center cutout, score all sides then score diagonally to opposite corners. Flex the diagonals by hand and carefully force a snap along the diagonals. Then, flex these pieces to remove the now triangular sections. Result, a clean inner opening with minimal cutting effort. The remaining paper & residual rubber cement is easily peeled off. Square off any rough edges with a file or sanding block.
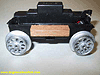 Click for larger picture
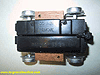 Click for larger picture
| Begin assembly with the bottom plate. The body needs to be secure on the motor block and yet removable for battery access. The example S-2 has one mounting solution. Epoxy 1/4" sq. hardwood strips about 1" long to the motor block centered and mounted flush with the top of the open motor block. Scratch diagonal lines on the motor block under the mount area prior to the epoxy step. This gives the epoxy something to "bite" on with the smooth plastic. Corresponding 1/4" strips are epoxyed to the top of the bottom plate flush with the opening. Length is not critical but should be at least the length of the opening. Do the same pre-epoxy scratch. |
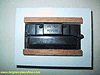 Click for larger picture
| Small brass wood screws hold the two sections together. Two are enough, offset to clear the motor block slide switch. Drill the motor block screw holes oversize and bottom strips undersize for a snug screw fit. Assemble the remainder of sections using your favorite styrene cement. A thin liquid type lightly brushed into the joints with a fine paint brush works best. The sides mount to the outside of the 1/4" strips. The ends are sized to fit inside the side pieces. The rear end piece is recessed 1/16" to provide a corner to mount the rear handrail. If you wish to detail the control cutouts in the top, cut them out before mounting the top. Top mounts flush with the front and equal overhang on the sides. Rear will just cover recessed rear plate. |
Bend the handrails from 1/16" brass rod, using the full-size pattern. An easy way is to bend the rod around something circular of about the same diameter as the pattern. When the curves are OK, mark and cut the bottoms to length with a razor saw or Dremel cutoff wheel. Epoxy the rear hand rail into place against the rear plate. Cut the front uprights from scrap 0.030 styrene, depth about 1/8". Drill tops 1/16" and thread onto the hand rails. Measure and drill 1/16" mount holes in the bottom plate, then install the front handrail and uprights. Fabricate a piece of angle from scrap 0.030 styrene and install as a horizontal bar near top of front handrail between uprights.
Continue with details. The radiator was cobbled together from bits of scrap styrene. It mounts in the front opening. The control levers can be cut from thin sheet metal or styrene. The metal will withstand handling better. Cement a scrap of styrene under the control cutouts and epoxy or ACC the levers in place.
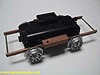 Click for larger picture
| A speeder needs to be turned around to go in opposite direction or to be removed from the rails when a train is coming through. Review the prototype CRRR image and notice the horizontal bars under the body front and rear. These can be represented by wood strips epoxyed to the motor block. Strips 4 1/8" long look about right. Thickness is not critical. 1/8" depth is about right. Check the plastic sleeved axles for clearance before epoxying in place. Slightly notch around the axles if necessary. Drill ends 1/16" before mounting. When the epoxy cures, install the 1/16" brass rod horizontal bars. This completes the construction, unless you want to add brake detail. I did not. Fussy little details have a way of falling off. |
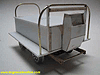 Click for larger picture
| Your speeder needs a paint job and an operator. Many speeders were yellow or orange but this is your choice. The CRRR image is an 'as found' that had not operated for some time. Operating prototypes were not this ragged. |
An ideal 1:20.3 operator can be formed from a Lanard "Corp" figure found at many of the same places you found the Stompers. These guys scale out a little over 6' and have articulated arms and legs. Pick one out and configure him as an operator. He can have a hand on a control. Once configured, dab a little epoxy in the articulated joints. When cured, fill the joints with spackling compound. Smooth off when dry with files and sandpaper. Paint the figure as you wish and mount him on the speeder with a bit of epoxy or mounting putty under his hips.
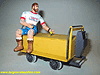 Click for larger picture
| Install an AA cell and enjoy your little machine. It will run over an hour on a NiCad or over three times that with a Metal Hydride. Beware, one speeder is never enough. Build a gaggle of them. They are fun and easy. |
Top of Page
|
|
|
IMPORTANT LINKS
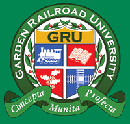
Get Your Official Diploma
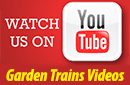
Watch New Videos
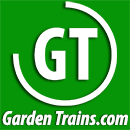
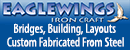
New Products Online
|
|